Solutions
Handling
Ergonomic efficiency
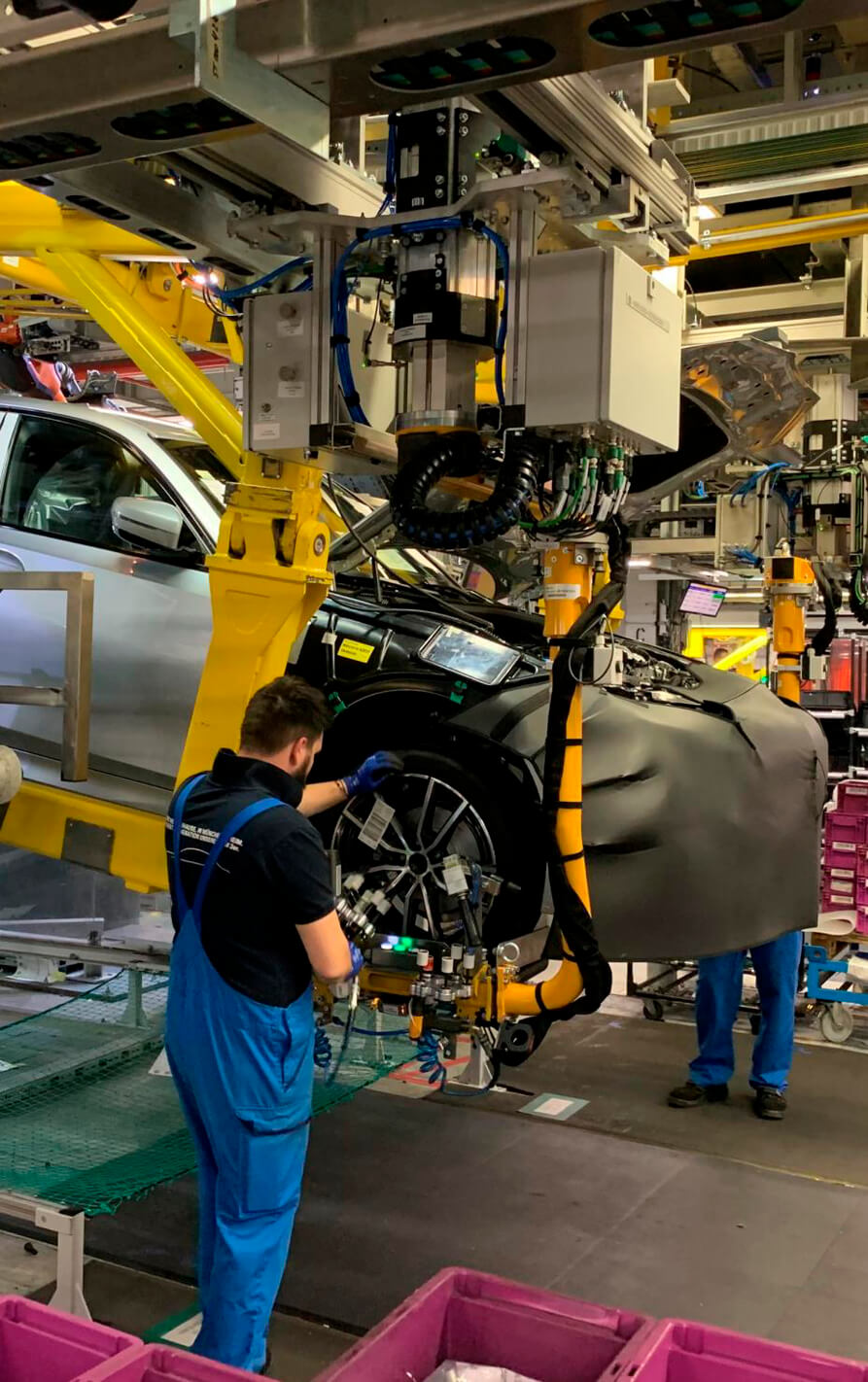
Joining wheels weighing up to 40 kg to the wheel hub in intervals of less than 30 seconds and fixing them with 5 screws is not only physically but also mentally demanding for the operator. In addition to enormous physical exertion - every day, some 4,400 wheels are assembled in this production section, moving a weight of 130 tons - a sense of proportion and feeling are required. The slightest carelessness inevitably leads to damage to the expensive aluminium rims, to components of the high-quality brake system or even to the metallic paintwork of the wheel housing.
Key components
- Wheel feed via inclined plane with separator and transfer arm
- Ceiling-mounted lightweight crane guidance system with linkable, steplessly controlled travel drives for autonomous as well as operator-guided linear movements lengthwise and crosswise to the assembly line
- Telescopic lifting axis with integrated, electro-pneumatic balancing system for controlled as well as operator-guided positioning and joining
- Disturbance contour optimised boom with roller-mounted wheel receiver and ergonomic operating and guide handles
Lifting technology
Gentle load guidance
In conventional crane construction, loads are always suspended from a hook and lifted by wire rope or chain hoists. In order to safely prevent the load from swinging when the crane is moving, speeds must be reduced on the one hand and starting and braking must also be greatly throttled. These circumstances slow down the manipulation process and thus cost time and money.
We offer an alternative in the form of trolleys with rigid load guides. For this purpose, we have a diverse portfolio of lifting units derived from the following basic types:
- Telescopic lifting axles
- Carriage lifting axles
- Double mast lifting axles
- Articulated arm lifting devices
The modular architecture of our constructions allow ceiling- or floor-mounted solutions in both stationary and mobile versions. An American customer therefore said:
"You get more than a crane but don't pay for a robot"
What to do if spatial conditions do not allow the installation of a standard lifting station?
Clean room requirements as well as aggressive dust deposits in the raw material preparation for silicon wafer production meant an additional challenge in the development of this special lifting and tilting station. With a servo-driven lifting spindle axis and compact infeed tilting mechanism, we finally created a system solution whose installation requires only Ø35cm - hardly more than the lid of a frying pan.
Key components
- slim, servo-electrically driven slide stroke axis with spindle drive
- Lifting slide in compact design with integrated feed, tilting and gripping mechanism
- automatic function sequence for lifting, tilting, emptying with integrated safety technology
Bolting
Target secure connection
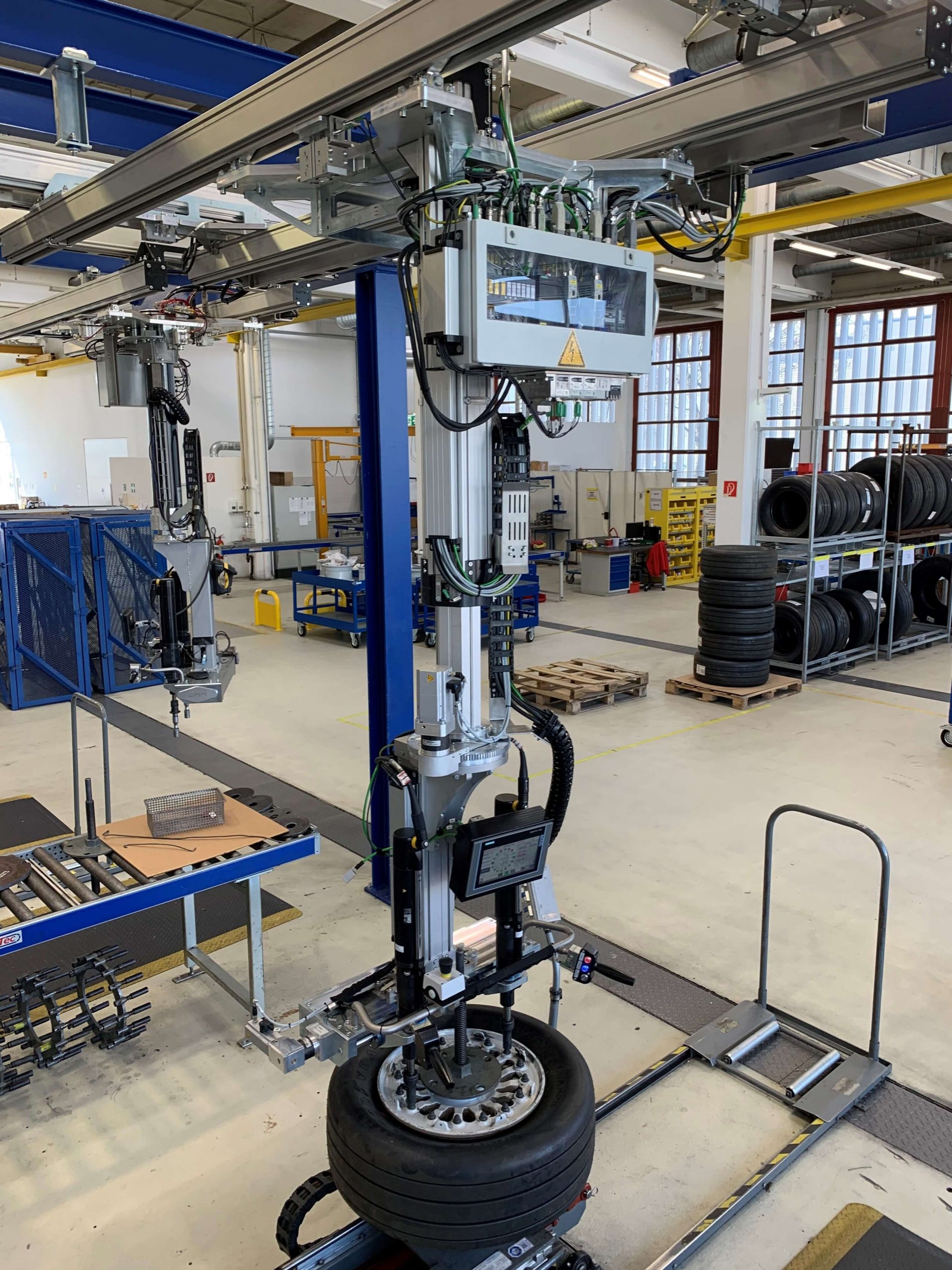
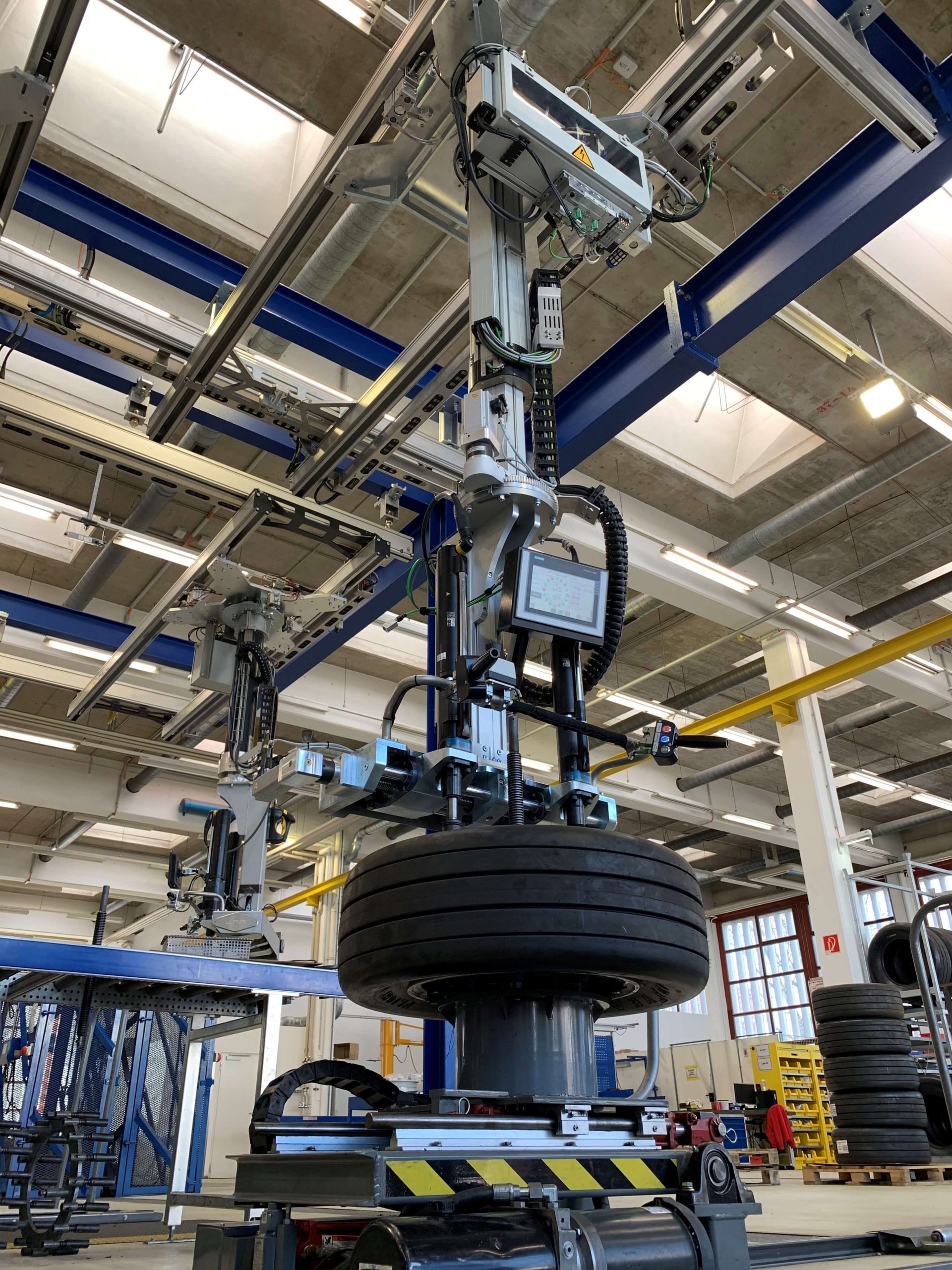
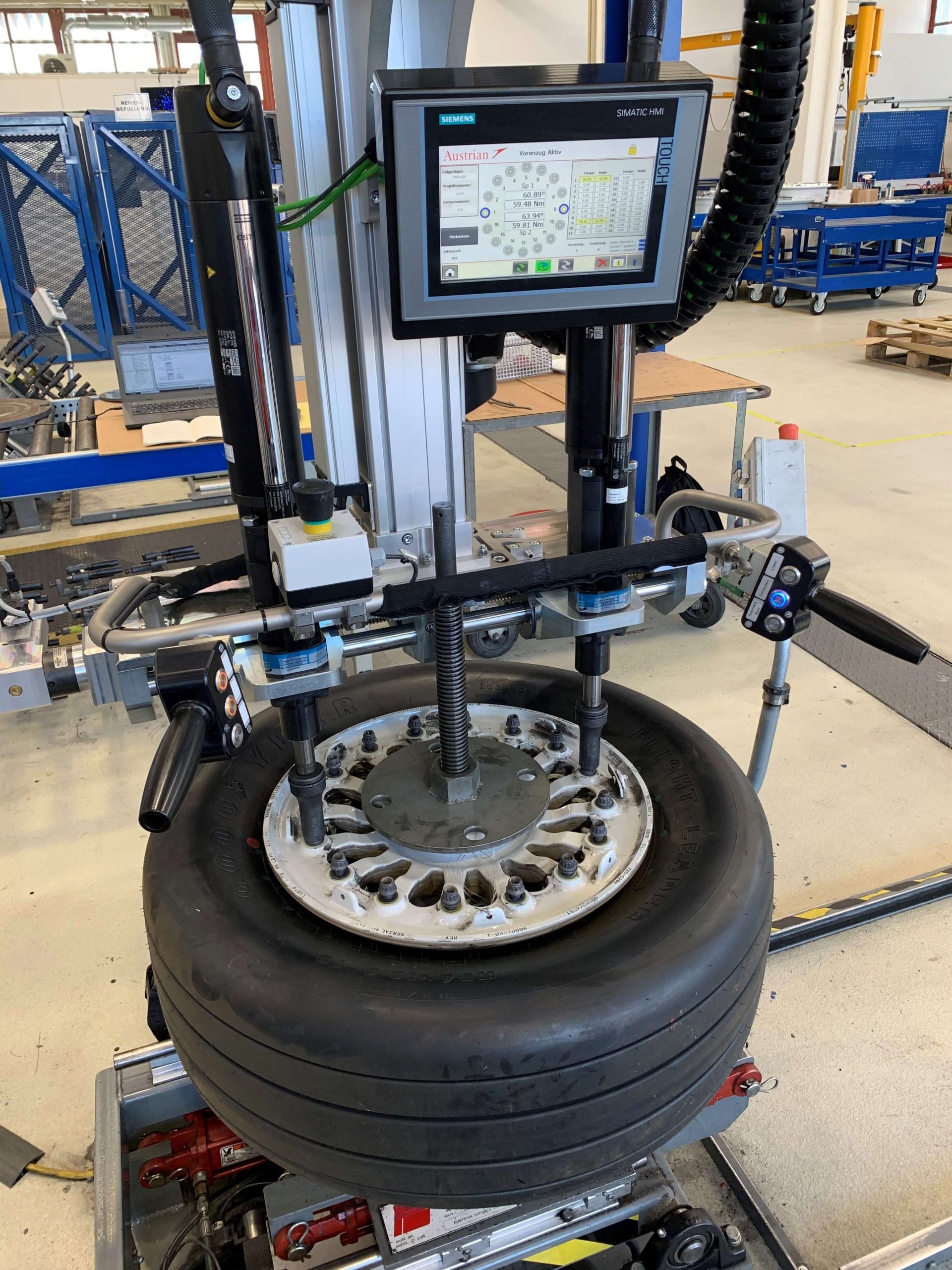
Every day, more than 10,000 aircraft wheels touch down on the runways of the world's largest airports. Naturally, the comparatively small wheels are subject to a great deal of wear. After 500 landings at the latest, the regular tire change becomes necessary. The MRO units in the shipyards carry out this task conscientiously, reliably and efficiently - so we can always sit on board with a good feeling and take off for distant lands!
After disassembly, cleaning and 100% inspection of all individual parts, the new tires are mounted on two-piece rims. Depending on the aircraft type, these rims have from 12 to 22 bolted joints on different pitch circles. These must be bolted according to the manufacturer's specifications with a 2-step tightening procedure.
The system design as a dual nutrunner with integrated nutrunner positioning system reduces the process time by more than half. This ensures fully autonomous execution of the screwdriving process in automatic mode, including logging of the result data - higher productivity with better quality.
Key components
- Ceiling-mounted lightweight crane guidance system for precise, operator-guided linear movements to the wheel position
- Telescopic lifting axis with integrated electro-pneumatic balancing system including rotatable double screwdriver holder for automatically timed or manually guided placement on the screwdriving point
- EC screwdriving spindles with computer-controlled screwdriving process sequence and seamless monitoring of torque/rotation angle specifications